Our team is here to support you and solve your power challenges. Connect with our responsive experts today to learn about our customized power solutions and products.
Series 2400 Modular Rectifier (6 V - 600 VDC, 37 A - 36,000 A) Water-Cooled
The Series 2400 is a modular, water-cooled, primary SCR, DC power supply. The Series 2400’s modular configuration provides expandability for increasing future capacity of the unit, as well as redundancy for “fail safe” reliability and reduced downtime.
Applications
- Electro-coating
- Anodizing
- Electro-machining
- Electro-refining
- Plating
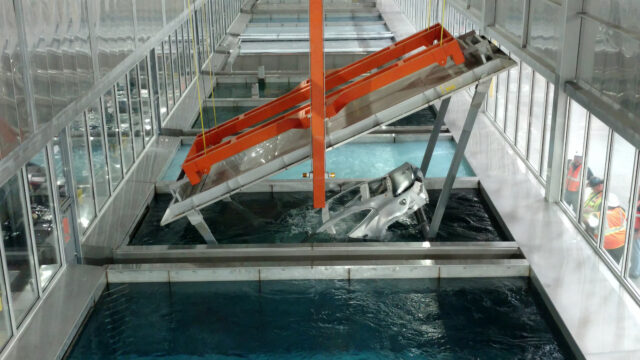
Product Specifications
Basic Specs
- Input AC Voltage: 208V – 600V
- Output DC Voltage Range: 6V – 600V
- Output DC Current Range: 37A – 36,000A
Features and Benefits
- Significantly reduced downtime
- Modular expandability
- “Fail safe” reliability
- Water-cooled
- Simplified maintenance
- Completely automatic
- Small footprint
Performance Specs
- Input Line Variation: ± 5% from nominal
- Voltage Regulation: ± 0.5%
- Current Regulation: ± 0.5%
- Operating Range: 0°C – 40°C
- Efficiency: 85% – 93%
Frequently Asked Questions
What are the advantages of a modular rectifier design?
The modular rectifier design incorporates multiple modules on the output of the rectifier, connected in parallel, which share the output current of the load. This paralleling of modules provides an increased defense against costly down time for production. If there is a failure with one of the modules, then a dedicated circuit breaker connected to the module will trip, and the unit will automatically de-rate its output current capability. This condition will allow you to run at reduced capacity instead of going down completely; which is what happens with conventional rectifiers. If a redundant module is purchased and installed in the rectifier and then a module failure occurs, you will be able run at full capacity with no downtime. Another advantage of the modular design is that it may be also purchased with expandability. This means that additional modules may be purchased and installed in the future, which will increase the current capacity of the rectifier if production demands grow.
How can I reduce or eliminate down time?
With a modular rectifier, downtime can be reduced if a redundant module is purchased and installed. For further protection against downtime, a second rectifier and a DC switch can be purchased. Therefore if a rectifier goes down or is being serviced, the backup unit can be brought online within a few minutes. For more information, see our Options document entitled u0022DC Transfer Switchesu0022 for details about DC switch and backup rectifier configurations.
What size rectifier do I need?
Rectifier sizing has many variables including part size, anode cell surface area, chemical / paint characteristics, and process time. The chemical / paint supplier, or the finishing system supplier usually recommends the rectifier size required for the application. In e-coat, the output voltage of the rectifier is usually 400V or 500V maximum. As a general rule of thumb, output current is usually 2.5A per square foot of metal, for 2 minute dwell time, with film build of 1 mil of paint.
Which is better: air- or water-cooling?
The environment where the rectifier will be placed usually determines the best type of cooling. For harsh, corrosive, or high-temperature environments water-cooling is best suited.
Which leg of the rectifier is grounded?
The rectifier output is isolated, allowing either leg to be grounded per process requirements.
Can I control or monitor the rectifier with my PLC?
Yes. As an option, Controlled Power Company offers single channel computer interface cards for monitoring and/or control of the rectifier. The computer interface card can be configured for 0 to 10 volt, 0 to 5 volt, or 4 to 20 mA signals. Additionally, we offer integrated distributed I/O modules so that communications with the PLC can be performed over Ethernet or serial connections, instead of running analog signals.
How can I reduce the floor space needed for rectifiers used in my process?
Controlled Power Company can custom design rectifier cabinets for limited floor space, single side access or provide multiple units in one enclosure.
Do I need a separate feeder transformer for the rectifier?
The rectifier does not require a separate feeder transformer; however, depending on site requirements, one may be needed. Please consult an electrical contractor or a consultant for further information.
When do I need a DC switch?
A DC switch is used for isolating the output of a rectifier and may be configured for various applications to reduce downtime. When downtime is unacceptable, a DC switch connected to the normal production unit and a standby unit provides a quick means of switching between the two in the event of a failure or for routine maintenance. The DC switch ensures that DC power is not present in the rectifier, so that it can be serviced safely by repair personnel. While the down unit is being serviced, the other unit will operate normally. You will not need to shut down the line when servicing the rectifiers. For multi-zone operation, there are many different configurations for DC switches. The most common is that a DC switch enables one rectifier to supply power to any zone. This can be either of the two primary rectifiers, or even a standby. A DC switch may also be configured to switch one rectifier between multiple tanks.
How can I increase my rectifier current output?
If you have a modular system that was purchased with expandability, you need only to install additional modules for additional current. If you have a non-expandable unit, another unit may be connected in parallel. The parallel control option will allow both units to equally share the load current. Some changes to the existing unit may be required.